- Mold Design
- Savings in terms of production value:
- Time to market can be reduced:
- Better performance:
- Related Tags : Mold Design
Why Mold Design Services Are Critical For Custom Manufacturing Success
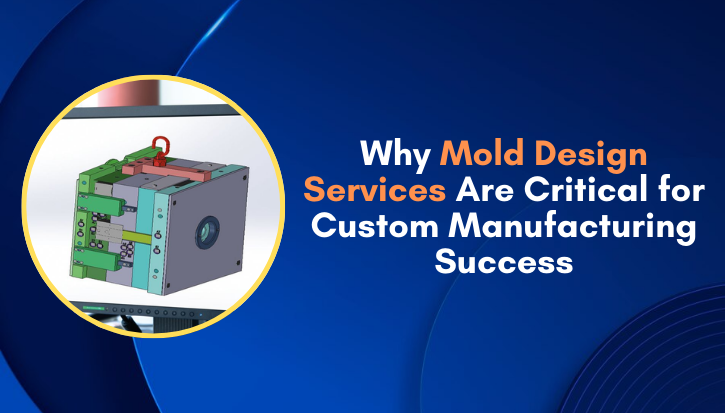
Presently, most industries express diversification and emphasize custom manufacturing. These manufacturing sites produce tailor-made solutions in line with the preferences and needs of a particular client. Such production allows businesses to create products that must be unique, efficient, and competitive in the ever-changing market. The centerpiece for such manufacturing lies in the most crucial process: mold design, from which high-quality, precision-engineered parts are obtained. Effective mold design ensures that each component is manufactured to exact specifications, reducing waste and minimizing production demands. Manufacturers can achieve optimal results by focusing on Custom Mold Design, streamlining production processes, and providing innovative products that meet market demands. In this article, we will discuss why mold design services are critical for the success of custom manufacturing, the factors making mold design practical, and the advantages it has for business.
Understanding Mold Design Services
Mold designing services include all the processes involved in designing molds, which is again a need of the hour for custom part manufacturing in various manufacturing applications. Custom manufacturing services play a pivotal role in custom manufacturing by ensuring that the mold is done based on the project's requirements. Thus, customization involves material selection, parts to be produced according to their geometries, and production volume, which is significant while fulfilling functionality and performance in the final product.
Expert mold design services provided to manufacturers result in efficient and quality production. This is because the output from a good design minimizes waste material, reduces cycle time, and provides an accurate replication of complex geometries. This results in an enormous consistency in product quality attributes that are highly necessary to meet industry norms or the expectations of customers. In addition, the practical design of the Custom Mold Design facilitates streamlined workflows in production, enabling faster turnaround times and not associated with the value of rework and defects. It is an essential investment for manufacturers looking to optimize their processes to provide quality and reliable products.
The Role of Plastic Injection Mold Design
Plastic injection mold design involves specialized mold-making operations. The goal is to build molds used in the plastic injection molding process, where hot plastic melt is injected into a mold cavity, then cools and solidifies into the desired shape. To this end, the designs of these molds are highly critical in that they will influence the production quality, production rate, and outlay.
A well-designed Plastic Injection Mold Design produces parts with maximum precision, minimal defects, and minimal breakage. Proper design helps avoid the probable problems of warping, shrinkage, or non-filled cavities that may slightly hamper the functionality and aesthetic appearance of the finished product. Furthermore, a maturely designed mold maximizes the cooling and ejection stages of the injection molding process, which increases the speed and reduces cycle times during production.
From a value standpoint, efficient injection mold design minimizes material waste and maintains sufficient strength for high-volume production applications without causing the mold to wear out. This does much in its own right to help manufacturers maintain low value over constant repairs or renewal. Generally, plastic injection mold design is essential for the mass production of good quality, inexpensive products; therefore, it is an integral part of any successful custom manufacturing operation.
Factors Influencing Successful Mold Design
Good mold design combines factors used to produce high-quality, custom parts. In particular, the selection of materials, complexity of design, and precision engineering are the critical factors determining the mold-making process's ease and results.
Material selection This is the most critical factor in the durability and functionality of the mold. The type of material used in producing the mold and the end product determines the mold's lifespan and the parts' quality. For instance, molds produced using high-grade steel or aluminum may withstand heavy-duty production; hence, they are productive for long periods and maintain their performance characteristics. With custom mold design, the proper materials ensure that the mold will satisfy requirements for strength, heat resistance, and wear tolerance depending on the specific application.
Another essential consideration is Design complexity. Intricate product designs have to be balanced with manufacturability realities. Molds with complex designs and detailed features must be simplified and require much additional effort in the production techniques. It might increase the outlay of production. However, it is possible that a good mold designer can optimize the mold so that the intricacies do not compromise output efficiency. This is precisely where an experienced Mold Design Company becomes necessary as they guide you through the intricacies while balancing with reality.
Lastly, precision engineering ensures that your mold realizes the tight tolerances and accurate dimensions. In manufacturing parts that require an exact fit without any room for error in assemblies or meet almost absolute specifications for special applications, this level of precision assures producing fewer defects and a higher-quality final product, leading to the success of a project in custom manufacturing.
Benefits of Professional Mold Design Services
Using professional mold design companies presents several advantages to manufacturers regarding manufacturing process improvement. A company can gain much with professional services through mold design services if they benefit from the following significant advantages:
Expert designers will first optimize molds to minimize material waste and defects created during production. A well-designed Custom Mold Design leads to fewer production errors, significantly minimizing values incurred in rework and scrapped parts. High-quality molds also have longer useful lives and do not require frequent maintenance, minimizing operational levies over time.
Professional mold design companies use highly advanced tools and technologies to speed up the process of designing a mold. This allows for quicker iterations and approvals, meaning manufacturing can speed up production timelines. Businesses reduce the time spent finalizing a mold and beginning manufacturing, enabling them to hit the market more quickly and gain a competitive advantage.
The professionals will design a custom mold for the final product to meet the specifications. From complex geometries to tight tolerances, expert designers create molds that improve the functionality and aesthetics of finished parts—consistently achieving or exceeding product expectations results in improved product performance, higher reliability, and better customer satisfaction.
With all these benefits integrated into them, professional mold design services are a necessary element of your business if you want to make it easier for yourself in the manufacturing department and gain success in developing custom products.
Case Studies
A good mold design project has given examples of how the right approach makes a difference in custom manufacturing. For example, an automotive parts manufacturer sought precision-engineered components to work with a high-performing vehicle. By teaming up with one of the highly reputed mold design companies, the manufacturer designed an optimized injection mold design that could manufacture complex parts with significant tolerance accuracy. After all these changes, a decreased percentage of defects during production coupled with a faster assembly time, thus resulting in inexpensiveness and quality.
A medical device manufacturer struggled to create complex parts with fine details. In close collaboration with mold design experts, they developed a custom mold that would provide the parts as needed with extreme precision. This expedited the time to market for their new product line, giving them the potential to gain a competitive edge in an increasingly regulated industry.
These projects will teach one the importance of collaborating with experienced mold design professionals. Best practices include early involvement of the mold design team in the product development phase, manufacturability of designs, and continuous testing throughout the mold development process to ensure that any potential issues are addressed before full-scale production. This all amalgamates with general success in custom manufacturing by providing quality products efficiently and reliably.
Call To Action
At 3D CAD Design Service, our committed team is always at the forefront to bring your ideas to reality through personalized solutions that help satisfy all your requirements. Our exceptional services make our valued clients return to us, and this makes us proud of our own selves. If you're ready to take your ideas to a whole new level with a commitment to greatness, please do not hesitate to contact us today! Please call us at +1 (647) 294-5240 or e-mail us at [email protected].
Conclusion
Mold design may be a critical factor in custom manufacturing, especially in its overall impact on final product quality, production efficiency, and the bottom-line fare of operations. Knowing the significance of Custom Mold Design and its connection to Plastic Injection Mold Design helps us understand the influence of material selection, design complexity, and precision engineering as influencers toward accomplishment. The following provides enormous value savings, reduced times to market, and better performance with professional mold design services, which are invaluable to businesses that want to produce high-quality, reliable parts.
Partnering with an experienced Mold Design Company assures manufacturers that their molds are optimized for efficiency and precision, ensuring they remain competitive in today's market. In addition, as a business looks to raise the quality of its production process, investing in professional mold design services is one wise decision that ensures long-term success and customer satisfaction.