- Mold Design
- Related Tags : Mold Design
From Idea To Reality Why Custom Mold Design Is Key To Your Success
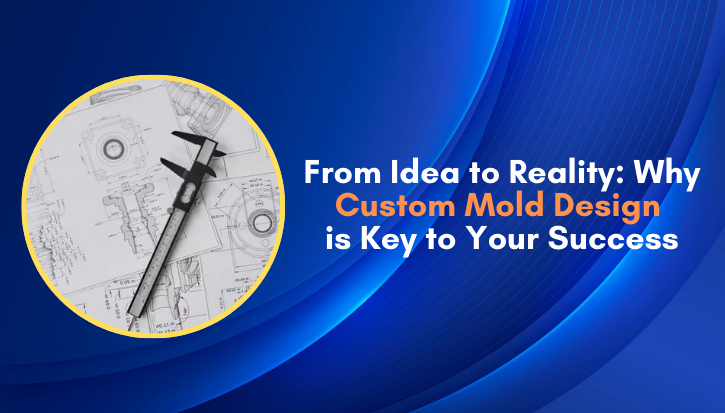
Custom mold design has been critical to the production process within the manufacturing sector. It makes products that reach the desired quality, functionality, and precision. For delicate parts or large-size components, the accuracy of a mold design is as critical as its end product. Custom mold design is especially critical since it allows the manufacturer to design specifically for the specific product's needs, the materials to be used, and the production goals. Each product will perform as desired, with fewer defects and increased efficiency.
With a custom plastic mold design, manufacturers will get great tailored solutions perfect for unique applications. The molding procedure from idea to production works ideally with flawless execution of the mold design so that innovative concepts are translated into real and functional products. In this respect, no possible communication or exchange can be overemphasized because the custom approach directly affects the product's performance in the whole market.
Principles of Injection Mold Design
Injection molding is the most popular method for producing large quantities of precision plastic components. It consists of injecting molten plastic material into a mold under high pressure, thus allowing it to cool and harden to the precise form of the desired product. Much effort has to be concentrated on the design of the mold itself to carry out successful injection molding. The injection molding mold design will help produce accurate repeat parts in proper cavity shape and size. A good design is needed to avoid defects, and uniform material flow to achieve high tolerance and produce good-quality output.
Precision is highly essential in the injection molding mold design. A minute design defect causes warping, incomplete filling, or high cycle time. The design of a mold should be customized to meet specific product specifications, choice of material, and required features. Advanced CAD tools such as AutoCAD mold design enable engineers to make detailed and accurate mold designs. Such tools allow for optimizing every part of the mold, including cooling channels, injection points, and so on. With auto CAD mold design and other specific applications, producers can now get precise and applicable molds to their needs.
CAD Tools and Technologies that Power Custom Mold Design
CAD, like AutoCAD mold design and SolidWorks mold design, is a computer-aided tool used in manufacturing accurate, detailed mold designs. Using such tools, the engineer can model and simulate all aspects of mold creation before it's ever physically produced. A virtual view of the mold allows manufacturers to determine and test configurations that may lead to a design flaw before the final product is created.
AutoCAD mold design is widely used in terms of flexibility and accuracy in creating both 2D and 3D drawings. It gives comprehensive drafting tools for designers to develop intricate designs, optimize mold features, and improve overall functionality. SolidWorks mold design stands on high values added by advanced 3D modeling capabilities and simulation features, allowing dynamic analysis as materials behave in the injection molding process. Such benefits may be accomplished using SolidWorks by simulating the material flow and cooling process and even detecting stress areas, thus creating more efficient optimized molds.
Both AutoCAD mold design and SolidWorks mold design maximize flexibility in every phase of the design process, including rapid changes or adjustments according to the product's specific demands. This accuracy and flexibility make a tremendous difference between correct performance in custom molds and false work in production.
Advantages of customized plastic mold design for specific product requirements
This makes customized plastic mold design valuable for improving the overall production of manufacturing processes, especially regarding the durability of the produced products, efficiency, and performance. Through customized plastic mold design, a company can design molds specifically made for a product's exact specifications. Customization improves the durability of the final product by optimizing the mold for its material and the application the product is meant for.
Furthermore, customized plastic mold design enables efficient production. With the excellent fit between molds designed precisely for a specific product, manufacturers could lower their scrap rates, cycle times, and all units produced. Such aspects lead to quality parts and wastage reduction, thus resulting in an overall streamlined production process.
In injection molding mold design, the capability to design molds to specific features, materials, and production needs has to be a must. For instance, in the case of fine details, complex geometries, or particular material requirements, it would be easy for specialized mold designs to cope with such factors. Injection molding mold design will exhibit precision in every product, reducing the chances of defects as the final products will meet the expected standards. Ultimately, bespoke designs allow manufacturers to develop high-performance products while still finding the best possible productivity within the line of manufacture.
How Stamping Mold Design Fits into the Customization Puzzle
Stamping mold design plays a crucial role within many manufacturing industries, primarily when high-volume production of precisely made metal components is in question. In a stamping press, materials like metals or plastics may be cut, formed, or shaped. These molds make it possible to produce complex and detailed parts that are highly required in the automobile, electronics, and appliances industries. High production rates can be achieved using stamping molds, which is why these molds suit standardized parts production on a large scale.
The design of a stamping mold is preferred where the parts required are in large numbers with negligible variations, which is the primary reason why manufacturers pick this process. Stamping molds, unlike regular machining, can manufacture thousands of millions of components with much tighter tolerances, which makes them an economical option for mass production. Stampings can also be designed with various materials, making the final product more versatile.
Among the various mold design services, stamping mold design is ranked number one when meeting the specific requirements of products. Whether parts require intricate shapes or metals or need to be formed into very accurate specifications, customization stamping molds ensure that molds are oriented according to a product's desired performance and design characteristics. By working with skilled mold design services, the manufacturers are able to fully utilize stamping molds, thereby bringing out excellent products at an exact and very rapid pace.
How Expert Mold Design Services Help in Bringing Ideas to Life
Specialized mold design services fill a significant gap between idea and reality. Advanced design technologies and specific knowledge are used to make molds that can meet the precise specifications of the product, thus ensuring the outcome is functional, durable, and inexpensive. Collaboration with experienced mold design companies enables producers to tap into expertise in optimizing designs for production efficiency and product performance.
Injection molding mold design and stamping mold design experience is very important in solving specific problems related to material flow, product geometry, and production speed. Professional mold designers could predict problems associated with flow and cooling in the material and make necessary adjustments for a smooth production process. With a strong cooperation relationship between a manufacturer and an experienced mold design service, optimal results can be reached in producing premium-grade products that meet aesthetic and functional criteria.
Call To Action
At 3D CAD Design Service, our committed team is always at the forefront of bringing your ideas to reality through personalized solutions that help satisfy all your requirements. Our exceptional services make our valued clients return to us, making us proud. If you're ready to take your ideas to a new level with a commitment to greatness, please do not hesitate to contact us today! Please call us at +1 (647) 294-5240 or e-mail us at [email protected].
Conclusion
Custom mold design for product development is essential because it provides precision and flexibility in shaping ideas into actuality. With a customized plastic mold design, manufacturers can be sure their products will meet the criteria, work flawlessly, and be manufactured at a reduced value. Investing in professional mold design services can help companies optimize their processes, reduce defects, and achieve quality products to their fullest potential. In the highly competitive manufacturing landscape, partnering with experts in customized plastic mold design is extremely important for a business's long-term success and growth.