- 3d Product Design
- MAXIMIZE SPEED
- CNC programming
- CNC machining
- Machine Control
- Mold simulation and optimization
- Related Tags : 3d Product Design
Avail The Best 3d Product Design Services
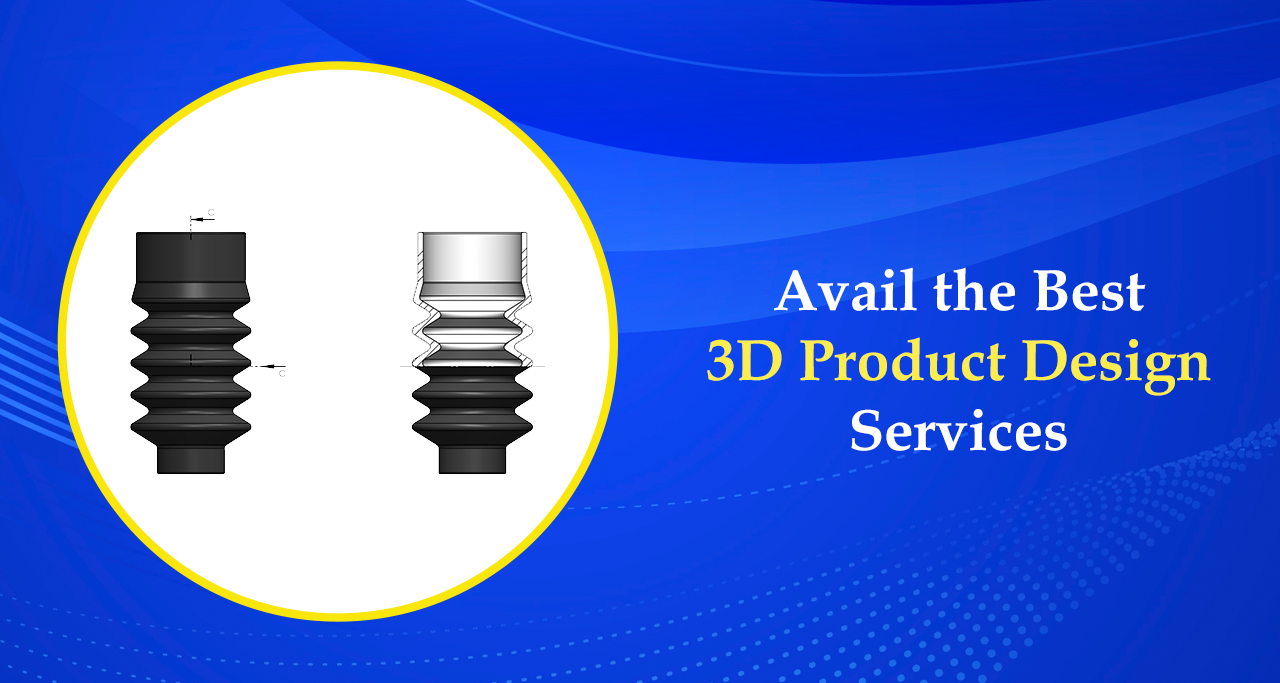
Your responsibility is to create reliable numerical control programs that run smoothly and produce accurate and reliable tools for 3d Product Design Services. Management expects you to complete these programs with the least amount of time and energy. Of course, they need you for several to schedule overlapping projects to run simultaneously, CNC machines are continuously fed and downtime is minimized.
Moving too fast and making a mistake can be disastrous. Your precious material may end up as scrap. User may be injured. An expensive cutter could be damaged. Or the entire CNC machine could break down, damaging\your bottomline, your production schedule and\your company's reputation with customers.
It may seem obvious, but the most important barrier to efficiency is the speed at which various stages of the molding process can be accomplished. Speeding up your work depends a lot on the software used to turn the designed product into a full mold which is done by Best 3d Product Design Services in Canada. Ideally, early adopter software can enjoy automating your work for three possible delays\geometry Moldmakers know that product design is a beast compared to 3D -with the tool used for that purpose. One way to speed up the transfer process is to automate the analysis and correction of the model
Implications When a Product or Material is First Imported into a New Market
Software designed specifically for mold\applications should be able to import the design and find problems with the product of malleable iron, such as insufficient tipping or backlash on the sides of the part. Many applications can go further by providing tools to automatically solve the most critical problems of 3d Product Design Services, such as fixing missing surfaces, repairing badly cut surfaces or adding deep pocket bottom radii.
Choosing software with very powerful algorithms gives your company a measurable speed advantage. Multithreading makes it possible to complete all programming steps faster thanks to advances in computing technology. The ability to create tool-friendly CNC strategies such as Non-adaptive cleaning allows parts to be processed faster and more efficiently in 3D Mold Design. Although many software vendors make similar claims about algorithms, ask to see how the software works with your parts before you make a decision.
During machining, you save time, which is the efficiency of the cutter in the machine immediately Software can help with this as well, as it allows moldmakers to create NC programs that automatically minimize retraction, especially during roughing. If a retreat is required, the software can ensure that the knife takes off as little as possible and moves to the next access point as quickly and safely as possible. All of this allows you to cut less air, reduce unnecessary movements and shorten cycle times
Strategies and Approaches to Significantly Increase Quality in Products and Services
Speeding up individual tool steps and workflow is not worth it if you have to compromise on tool quality and therefore the quality of the molded part with dedicated mold software, you don't have to make that compromise. Instead, you can use unique features that improve surface finish and make the process more efficient.
Many shops use timed control points to ensure process tools - especially large or complex ones are accurate. This may involve stopping the machine to measure parts of the workpiece with a caliper. Or may require the operator to remove the part from the CNC machine and take it to a special quality control department where coordinate measuring machines (CMM) are used to inspect the part. This process is both expensive and time consuming.
Benefits of Dynamic Machine Control in Enhancing Automation and Precision
Making molds with large, deep pockets can be a real challenge. These parts naturally have a higher\collision risk associated with the machine, cutter and/or workpiece. To machine these complex features, a molder can use a triaxial machine with long knives, but this increases the risk of tool bending or vibration, which can degrade part accuracy and surface finish. This choice will likely result in parts that require additional finishing, polishing and machining. A better choice is to use a five-axis CNC machine.
For plastic injection molding, simulation software provides a third way to maximize surface finish. Plastic parts may have some cosmetic defects, which are directly related to the choices made in mold design. Simulation allows mold makers to examine these variables and consider all options to reduce risks. You can get to know yourself. the types of process. to understand how gate options choices may change if you use gas assist,development, two shot technique, or change the packing and holding to grow the microcell foam
Measures for Protecting Equipment from Damage, Wear, and External Factors
The tool or machine head tip above is very inexpensive at worst. Crashes are not inexpensive to fix, they threaten the safety of CNC operators and can cause a lot of downtime. Dedicated software can also meet this challenge, allowing shops to increase workflow efficiency increasing the risk of damaging critical equipment.these things must be considered by 3d Product Modeling Company.